举全员之力,推精益生产,强企业体质
2011-3-1 0:00:00
我公司日籍专家丰田徹男撰写的题为"举全员之力,推精益生产,强企业体质"的文章在信质报上刊登.
原文如下:
绕线车间改善进展5月有余.期间,信质、瑞铃拧成一股力,以该车间为起点推行精益生产,真抓实干,成效显著.借此,我非常感谢信质各位同仁给予的信任与支持.
"立足精益生产,改善作业方式,强化企业体质",这是瑞铃多年来孜孜不倦的追求."强化体质"简言之,就是"明确生产流程,立足TPS基本思想,杜绝浪费,提高生产效率".这不单是生产部门的课题,更是公司全体的目标.
没有一帆风顺的改革
诚然,任何改革都不是一帆风顺的!推行精益生产势必在一定程度上改变原有的作业环境,对工人的作业方式提出了更高的要求,例如站立作业和多工序作业等.因此,员工抱有抵触情绪也在情理之中.然而,改善是为了最大效益地利用人力资源,绝非提高工人劳动强度.在日本,我也遇到过同样的问题,但如能加强沟通,问题也会迎刃而解.
当改善逐步推广开来,人们的不满将在改善所产生的成效中消失.而正是曾经的不满,帮助改革者发现了问题,并且找到了革新的智慧.
将生产周期缩短到极限
推行改善的一大重点在于"将生产周期缩短到极限".从经营来看,它关注尽早回收原材料和人工成本;在生产车间,则体现为如何以较少的资源投入获得更高的效益产出.
缩短生产周期作为改善的切入点,要求工序集约、流畅化,尽可能减少工序内外的"物";同时,严格遵守作业标准,积极解决各种新问题.
当我们深入到没有实施精益生产的一些工厂时,就会发现车间、仓库等场所库存堆积现象严重,且大多数员工处于点状作业的状态,这就大大削弱了企业的竞争优势.分析来看,生产周期长的主要原因在于"物"多,"物"越多,对于生产的异常现象就越不敏感,越无法准确判断,进而,生产活动减缓,4S水平下降,车间的精神面貌也搞不活.
生产周期改善必不可少的是"以JIT生产为基础,明确生产流程,彻底目视化管理"."目视化管理"包含了"管理标准正常-异常,一目了然"的体制和道具两方面,"目视化管理"的实施帮助改革者明确问题点推行改善.例如,物流上可设置工序内店面,确定库存基准,库存情况一清二楚;生产线可采用看板管理投产顺序、数量,生产进度可视化;用好标准作业票,通过彻底落实标准作业来构建一个轻而易举就能发现问题点的生产系统.绕线车间各生产线头所设置的生产管理板就是生产线QCD目视化绝佳的例子.
若能建立一个"减少生产现场的‘物',实行JIT生产,将生产活动限制在最少且必要的数量内"的生产体制,我想生产车间势必变得张弛有度,所有问题也将浮出水面.员工有了紧迫感,明确了需要改善的内容,工厂体质也必将得到强化.
改善贵在坚持
改善任重道远,需要人才和改善力.日本的经验是推广"自主研修",即由各部门成员组成的团队,在短期内集中就每月确定的课题实施改善,而生管、品管、保全等相关部门则要全力配合.如此一来,小组成员通过亲身参与、自我启发增强了独立改善的能力.改善不是要求他人做事,而是自我实践,从这点来说,信质未来需要培养更多具备改善能力的人才来助推企业的发展.
需要特别强调的是,一时的改善不难,难的是持之以恒.有些公司在半年或一年后倒退回去,主要原因就在于缺乏改善的连贯和持续性.
"改善需要执行力",只有上下团结一致推行精益生产,我们才能看到期待的效果.最后,让我们一起用不服输的态度和干劲朝着共同的目标迈进!
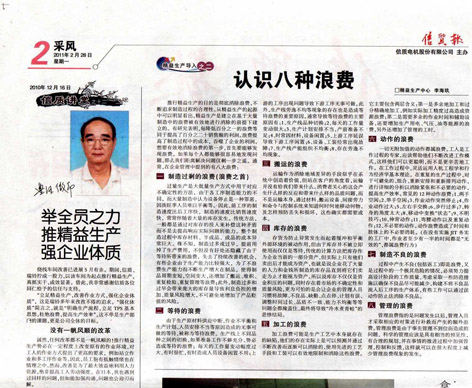
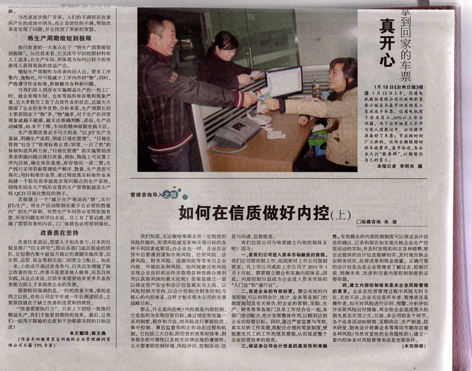